Editor's note:1st Lt. Moncada and Capt. Haywood were among a company of engineers who deployed to build treatment facilities in West Africa late last year. Now they tell their own experiences of soaking rain, midnight convoys, unreliable contractors and their "most valuable asset" — a Liberian captain. Here is their story:
From the point of notification to the initial push of the advanced party, the 104th Engineer Company (Vertical) had approximately 45 days to deploy the main body. Up to this point, the 104th, stationed out of Fort Hood, Texas, was preparing for a rotation at the National Training Center.
We saw the news reports about the spread of Ebola daily and we also heard the president's commitment to send troops and resources to West Africa, so our mobilization wasn't a surprise. For Army engineers, the scenario was perfect: deploy to an austere environment, conduct vertical construction, and provide timely assistance to people in need.
From the beginning of the project, we were confronted with daily challenges that made us better engineers and leaders. During previous deployments, most Soldiers in the unit had deployed to established theaters of operation, where there were reliable amenities and facilities. During this deployment we had neither, but were given the opportunity to face challenging situations and grow. Below are some of the lessons we learned along the way.
Once our brigade notified us that we were deploying, it was our job to ensure we had the right people and equipment to deploy in a short time frame. The two biggest factors in preparing for the deployment were personnel and equipment readiness. The number of people who became non-available through the SRP process was surprising. We experienced a 15 percent drop in our overall personnel readiness after going through SRP.
We learned that if the "SRP No-Go" decisions are not thoroughly vetted, deployable Soldiers could slip through the cracks and remain with rear detachment. Prior to notification, non-available personnel were a main focus point in our company training meetings and also in the battalion command and staff meetings. After going through SRP, arguing with health providers for deployment waivers, and adding combat engineers to the unit for the deployment, the 104th was at 103 percent personnel readiness.
Equipment readiness was another huge factor. All the minor fixes to vehicles, or all the spare parts that are still backordered, become significant stressors when you only have weeks to deploy. Luckily, our maintenance team carried an abundance of service kits for all of our vehicles. Our preparation still didn't keep us from spending long nights in the motor bay ensuring as many vehicles deployed as possible.
One might think to take only new vehicles, since they have less maintenance problems. That line of thinking is correct; however, a significant variable that initially gets overlooked is weight. Our newer vehicles (M1152, M1083A2P2) are substantially heavier than their older variants. The older models had more maintenance issues, but they were the only vehicles which could deploy via air transport, due to the cargo weight requirements. We would end up using the vehicles shipped by air exclusively for the first several weeks, while we waited for the equipment to arrive by sea. Overall, we were impressed with how many vehicles we were able to inspect, stage and deploy in a short time.
The concept of the Ebola treatment unit hinges on the idea of isolating patients and containing all waste and byproducts on the ETU site. The isolation is achieved by strictly controlling the patient flow. The overall site is split into two zones: a green zone and a red zone. The green zone is to provide health workers administrative space, latrines, showers, medical storage, water and fuel storage, and rest areas. The red zone is meant for patients who are either suspected of having Ebola or are confirmed cases. The red zone also has latrines, decontamination showers, contaminated waste storage, and a morgue.
The two zones are separated by barrier fences with gates, so that there is controlled movement from one area to the next. Waste management is achieved by digging V-ditches surrounding the entire site and also between the confirmed and suspected areas. That way no water from off-site runs on-site, and water on-site is channeled to safe locations, where the disease can die when exposed to UV rays.
After landing in Monrovia, Liberia, in mid-November, to our delight, we received the mission to participate in a joint ETU build. Our mission was to deploy 125 miles away from the brigade headquarters, located at the National Police Training Center in Monrovia, and construct a 50-bed ETU in Gbediah, Rivercess County.
The mission was to begin Nov. 30 and be completed by Dec. 24. We would not be conducting this mission alone, but executing it with the 1st Engineer Company of the Armed Forces of Liberia (AFL), commanded by Capt. Dada. He was previously in charge of two ETU projects, located in Sinje and Tubmanburg, and has served in the AFL for more than seven years. Capt. Dada's company totaled 40 AFL engineers.
Joint planning began several weeks prior to the start of the project. Given a project of this size and given the environment, it was crucial that everyone was on the same page. Therefore, the battalion arranged for a coordination meeting with all of the key players: leaders from the 104th, Capt. Dada and his platoon leader, the AFL military liaisons, our battalion command team, and representatives from the Defense Logistics Agency. Without meetings like this and the subsequent meetings over the phone, the ETU project in Gbediah would not have been as successful.
Our preparation paid off because once we received the mission, all the leaders had already been toiling over the designs and materials for weeks.
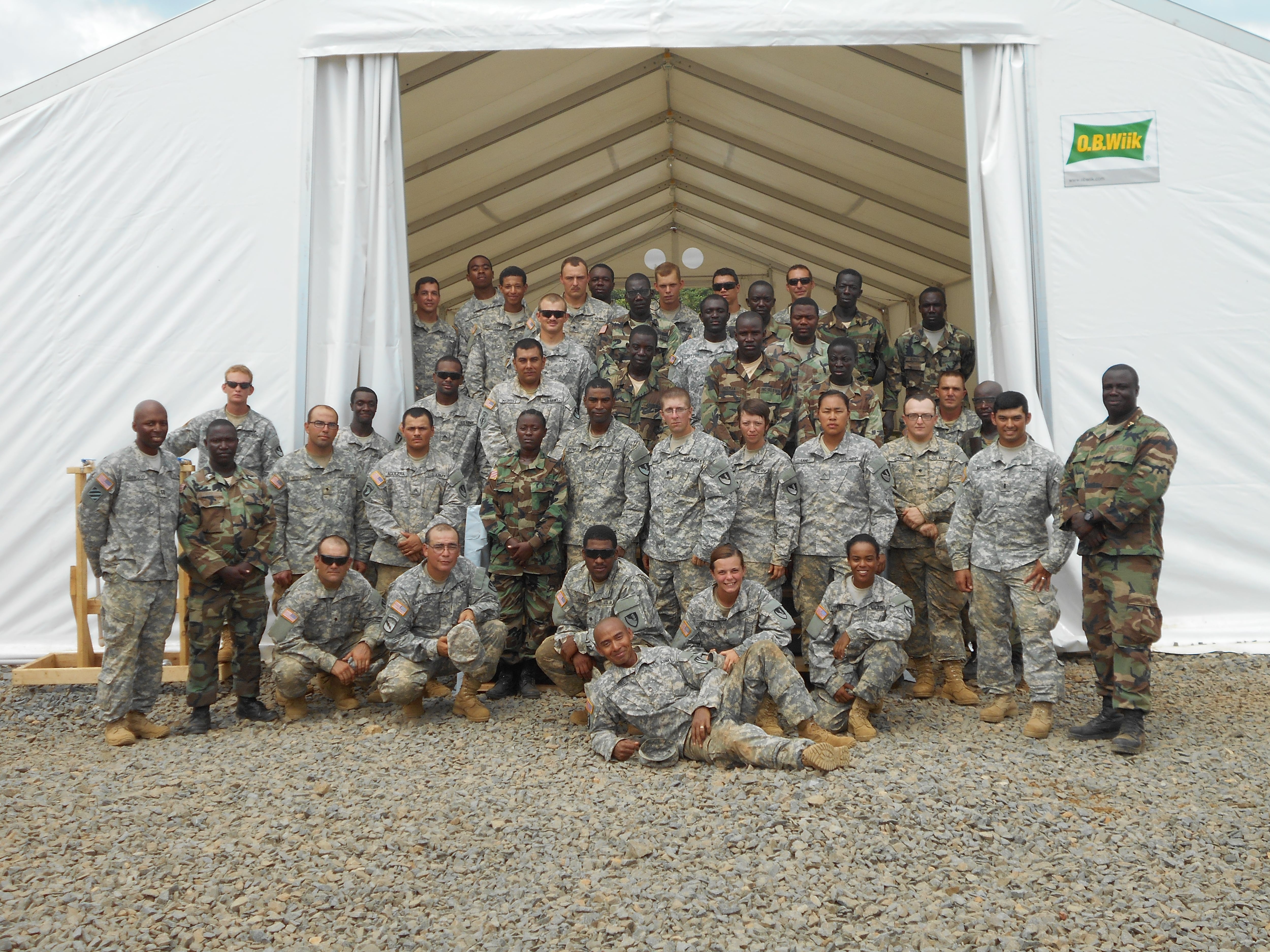
The 104th Engineer Company.
Photo Credit: Courtesy Jeremy Haywood
The initial advanced party was comprised of ten 10 Soldiers: the company commander, platoon leader, platoon sergeant, project NCO, three carpenters, one plumber and two surveyors. The AFL also sent a 10- Soldier advance party. The advanced party's main mission was to set up life support systems for the main body, oversee the contractors on the site, and begin prefabrication of vertical structures.
Due to AFRICOM's restrictions of driving tactical vehicles during high traffic hours, we were only able to move after midnight. The roads out to the site were barely passable, even at slow speeds. This delay in movement also mitigated the risk of accidents and allowed us to move alone on the narrow roads of Liberia. After the 125-mile convoy, which took six and a half hours, we arrived to the construction site. The advance party had 10 days before the main body of 50 Soldiers arrived.
Establishing an effective drainage plan was a constant problem throughout the entire project. The frequency and intensity of the rainfall was a factor most in the unit had never dealt with before. With rain comes lots of runoff. Since we were focused on clearing, grubbing, compacting and leveling the ETU site pad as soon as possible, we neglected the roads leading to the site and BOM areas. After several rainfalls and a multitude of vehicles traversing the site, the whole area became bogged down with mud and standing water.
Our contracted horizontal equipment would make temporary fixes on the roads, so that they could continue work on the ETU site pad. In hindsight, we should have focused more time on the service roads and work areas. The time spent conducting temporary fixes to the roads far outweighed the time it would have taken to complete the roads right away. In addition, the site layout made it difficult to implement an effective drainage plan. In the site design, the suspected area was down-slope from the confirmed area. Even though there was four to six inches of gravel covering the entire ETU pad, there was still a remote chance that there could be cross contamination between confirmed and suspected cases of Ebola, given a significant rainfall event. We dug V-ditches between the confirmed/suspected zones and the red/green zones, then backfilled the ditches with gravel so that the final grade was flush.
Modular construction was a key component of our ETU design. The building blocks for the majority of the structures on the site were pavilions. By piecing together pavilions or changing the orientation, we were able to make structures of varying sizes and purposes. We could very easily make all the walls, floor, and roofs for 47 pavilions and then stack them in our BOM area. If we would have erected the entire pavilion off site, there would only be enough space for approximately 10 pavilions. Due to the mobility of the pavilions, we were able to build everything off the actual site and transplant them into position once the horizontal work on the ETU site was complete. At other ETU sites, contractors waited for the horizontal work to be done before assembling any of the vertical structures, which added a significant amount of time to the project. On our project site, there was nothing to delay our progress. Having the ability to put the puzzle pieces together once on site was a tremendous success and ultimately allowed us to meet our deadline, despite setbacks and contractor delays.
The reliability of the contracted equipment and the competence of the contractors were one of our biggest problems on site. We were using the equipment hard and the equipment wasn't in good condition to begin with. When items broke, often the contractor would have to go back to Monrovia, easily a day-long trip, to procure parts, and the broken equipment would remain unused on the project site. There was no contracted site foreman to control and direct the contracted workers. With several tasks going on simultaneously it became a challenge to supervise the Soldiers and their work, while also overseeing the contractors. We eventually had to bring in two horizontal engineers from 615th Engineer Company to ensure the contractor was correctly performing the tasks to complete the site pad. Their job was primarily to assist the contractors, offer suggestions on best used practices, and ensure that the contractors were using the equipment efficiently the entire day. If the contractors weren't supervised in this manner, the equipment would sit idly by or the contractors would do the work improperly.
Working with the AFL was a rewarding experience. The Soldiers of the AFL are hard workers and having the opportunity for both parties to teach and learn from each other was a reward in itself. Capt. Dada had experience at ETU sites and knew common issues at previous sites. He was by far the most valuable asset we had.
Most of the issues centered on differences in constructions standards. The Soldiers were forced to explain and teach each other why their method of performing a particular skill was preferred, which forced them to internalize the basics and gave younger Soldiers more leadership responsibility. Constant communication is vital in preventing small misunderstandings that lead to much larger issues on the site. These problems were relatively easy to handle due to the nightly operations meetings attended by both groups. Both parties were able to express concerns and focus on the task, which was to complete the project under budget and on time.
Over the course of 22 days, the company deployed 30 Soldiers 125 miles, worked with 40 AFL Soldiers, and finished the horizontal and vertical work for an ETU site that was taking contractors 45 days to finish. Along the way we learned more about engineering and project management than on any previous project.